Филиалом «Гроднодорожник» КУП «Гроднооблдорстрой» в прошлом году приобретен новый асфальтобетонный завод, где производительность смесительной установки RD-130Х – 120 тонн в час при влажности материала 5%. О том, как он показал себя в работе, узнала корреспондент «ДБ» Светлана Смолей.
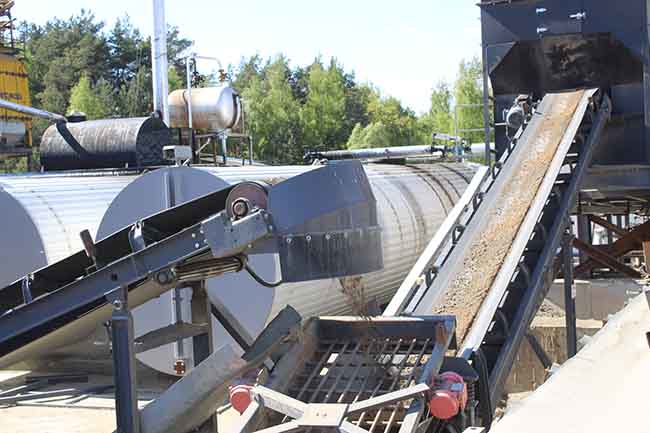
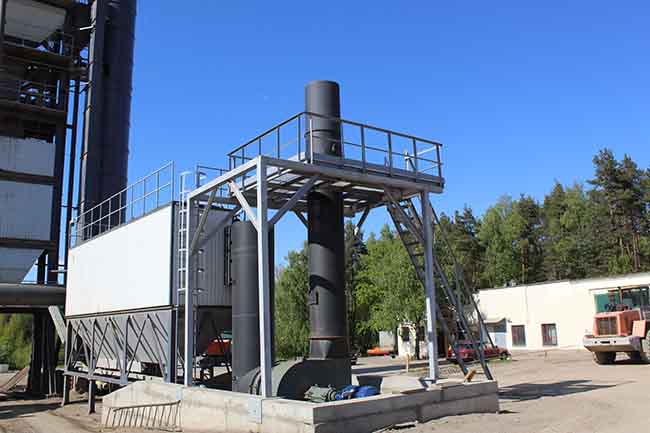
Подготовка площадки (залили почти метровый армированный фундамент), поставка оборудования, монтирование, подключение всех систем заняли порядка двух месяцев. Трудились в режиме 24/7. Пусконаладочные работы прошли в конце июня. С тех пор процесс идет технологическим чередом. Приготовление асфальтобетонной смеси контролируют три машиниста установки. Переучиваться им не пришлось, поскольку на предыдущем асфальтобетонном заводе ДС-185 было установлено похожее программное обеспечение. Прибывшие на шефмонтаж специалисты из Казахстана ввели белорусов в курс дела.
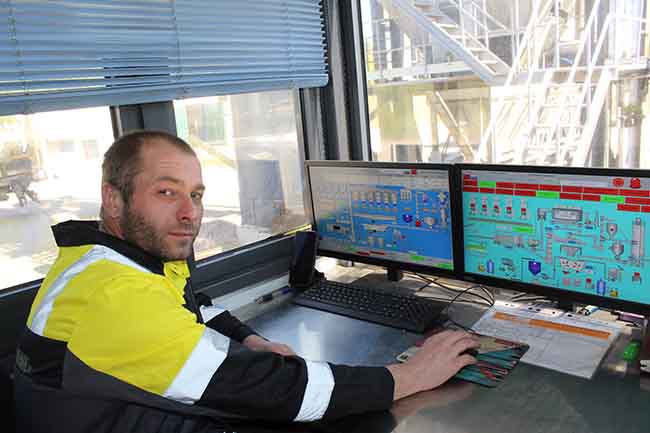
– В течение двух-трех дней научились управлению и стали работать самостоятельно. По сравнению с ДС-185 намного легче происходит смена рецептов, да и сама программа гораздо проще, – делится машинист смесителя Александр Малиновский. В «Гроднодорожник» он пришел два года назад. Трудился сначала на грохоте, потом на асфальтосмесительной установке. Специалист рассказал о процессе приготовления асфальтобетонной смеси.
В пять бункеров закладываются песок, отсев, природный и гранитный щебни. По двум конвейерам они направляются в сушильный барабан, где нагреваются до температуры 190–200 градусов. Элеватором материал поступает на грохот и рассеивается на фракции 0,5, 5–10, 10–20, 20–40. После этого нужное его количество идет в весовой бункер и сбрасывается в смеситель, куда подается битум. К примеру, для приготовления полутора тонн ямочной смеси требуется 79 кг битума. В течение 20 секунд идет смешивание – и машинист выбирает бункер (на 100 или 20 тонн), который наполняется готовой смесью. Если весь материал сухой, а не после дождя, то 20-тонный объем приготавливается за 10 минут. В нейтральном режиме температура в сушильном барабане держится около 36 градусов.
– При нормальной работе смеситель на компьютерном мониторе выделен зеленым цветом. А если происходит скачок напряжения, то начинает мигать. Завод рассчитан на определенный вольтаж и при понижении напряжения срабатывает защита. Когда на экране появляется красная полоска, свидетельствующая о нестабильности в сети, мы отключаем оборудование или это происходит в автоматическом режиме. Между тем на весах или в смесителе может остаться битум, тогда требуется слить его вручную, – в подробностях объясняет наш собеседник.
Появилось мигание на ленте – значит, в материал попали доски или камни, и к бункеру отправляется машинист для устранения лишних предметов.
– Здесь все крутится-вертится, надо следить очень внимательно за оборудованием. Битум, мазут накачиваю, масло доливаю, шприцую солидолом подшипники – их тут под сто штук, или работаю за компьютером. У нас полная взаимозаменяемость, – поясняет машинист смесителя Андрей Семенов, который пять лет трудится в филиале «Гроднодорожник». Был слесарем-ремонтником, затем – помощником и машинистом на 158-м смесителе. По его словам, новый завод отличается не только производительностью, но и условиями работы, хоть и на прежнем серверная была оборудована кондиционером. Сейчас меньше перерывов на ремонт, да и зарплата выросла. Обычно смена длится с 8 до 17, но в жаркую погоду они выходят в четыре-пять утра – так заботятся о тех, кто трудится на асфальтоукладке.
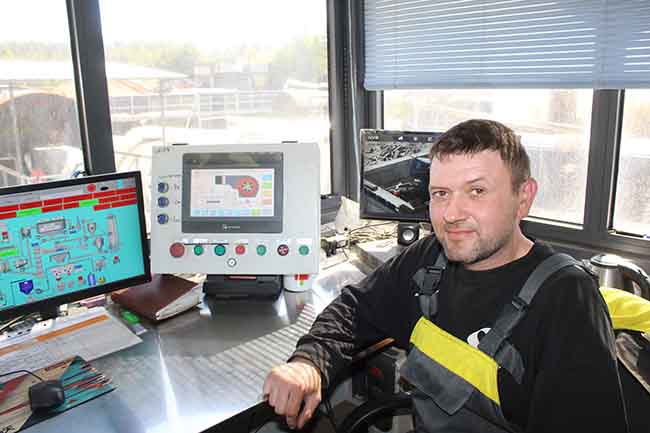
Начиная с июля, в 2024-м завод филиала «Гроднодорожник» выдал 82 тыс. тонн асфальтобетона, в то время как в предыдущие периоды на старой асфальтосмесительной установке было в два раза меньше. За март, апрель и май текущего года изготовлено около 30 тыс. тонн. Наилучший результат – в сухую погоду за 9 часов выпускали 1 тыс. тонн продукции.
Филиал производит и свои материалы для приготовления асфальтобетона, что положительно влияет на финансовые показатели. К примеру, щебень приготавливается на дробильно-сортировочном комплексе.
– За время функционирования завода заменили сменные элементы просеивания и сетки, когда выпустили 80 тыс. тонн. Они показали себя хорошо. Для сравнения: на грохотах и дробилках сетки меняем после 20 тысяч. Еще обновили некоторые подшипники. Надо отметить, что и броня после выданных на-гора более 100 тыс. тонн в нормальном состоянии, – отмечает прораб Вадим Дроздов, не забыв упомянуть и экологический аспект: – По основным выбросам – оксидов азота (NOx) и серы (SOx) – завод попал в категорию «ниже нормы», и это притом что работаем на мазуте.
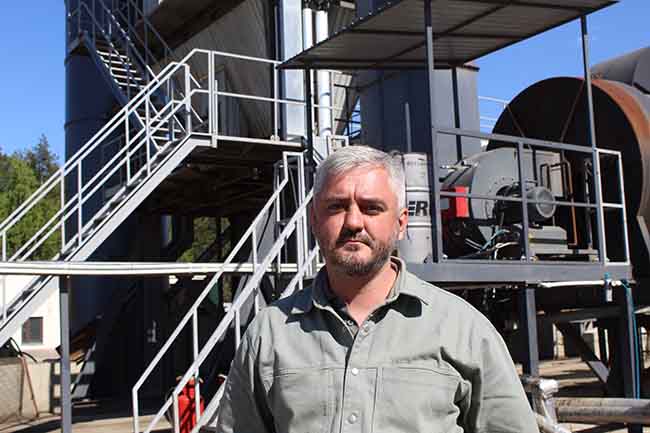
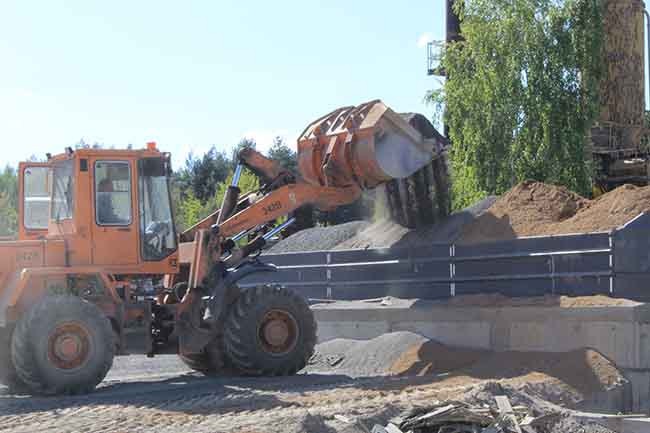
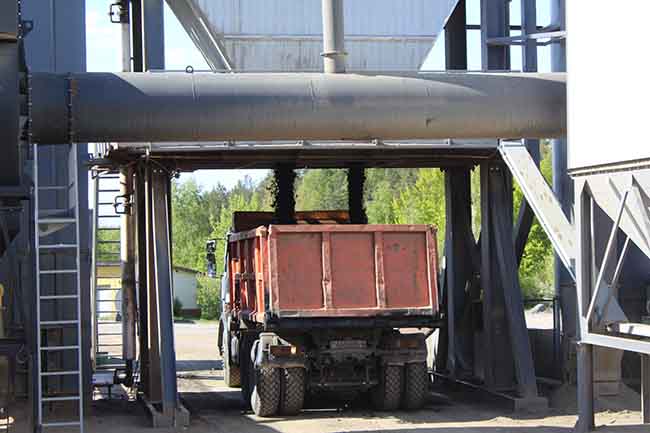
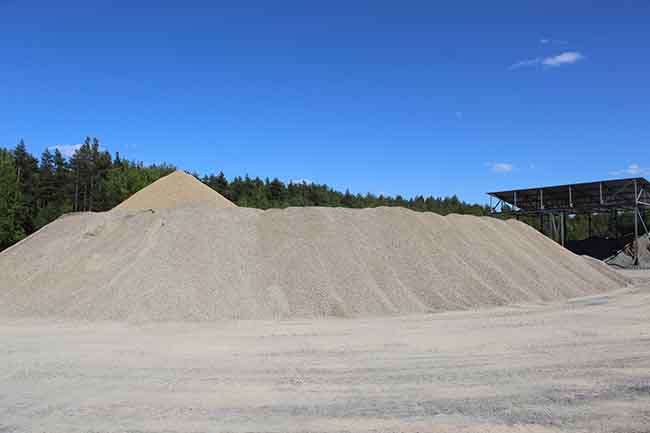
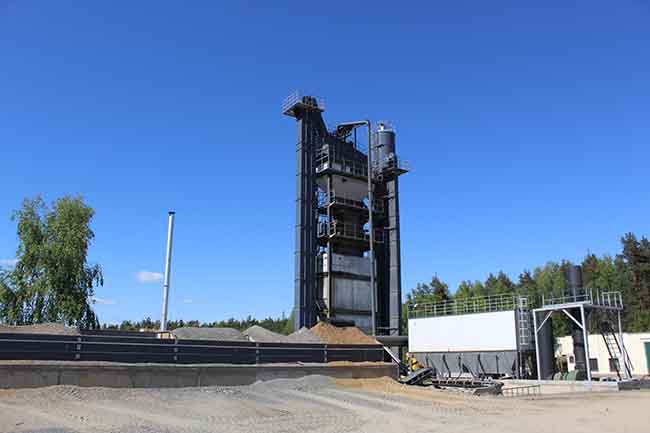
Завод оборудован фильтрующей установкой, которая собирает пыль, отряхивает ее и подает назад. Таким образом, даже мелкие частицы дополнительным шнеком идут обратно в асфальт. В рецептах используются специальные подборы, где добавляется в замес асфальта определенный процент пыли, соответственно, отходов нет. Процесс полностью автоматизирован в отличие от старых заводов, где требовалась предварительная просушка отделяемой пыли.
Выпускаемая продукция используется преимущественно при ремонте местной сети. Так, в апреле филиал укладывал асфальтобетон на дорогах Гродно – Заречанка, Гиновичи – Голынка – Сопоцкин, озеро Юбилейное – граница Республики Польша, Гожа – Цидовичи – Огородники, подъезд к деревне Новая Гожа. Кроме того, часть материала направлялась на объекты по прямым договорам, в основном, для предприятий агропромышленного комплекса, а также при осуществлении работ на республиканских трассах Гродненщины.
В этом году на территории асфальтобетонного завода для улучшения качества подготовки к производству были построены специальный заезд для фронтального погрузчика и новое место складирования фракции щебня после дробления. А отремонтированную дробилку разместят на площадке «бункерно», то есть таким образом, чтобы щебень не рассыпался буквой «п» и не перемешивался с другими материалами.
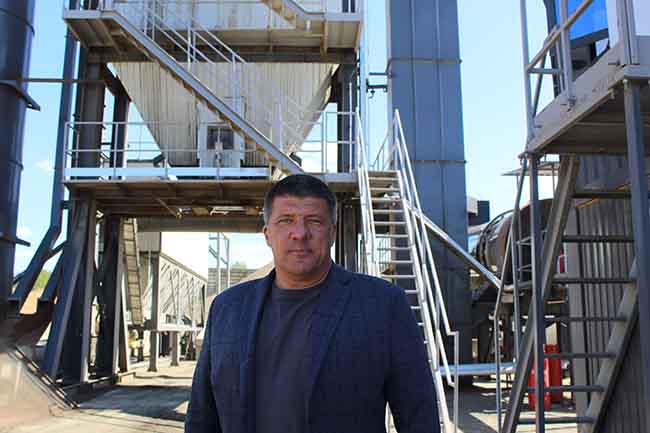
Владимир Король, начальник филиала «Гроднодорожник»:
– Постепенно идем к снижению расходов на выпуск единицы продукции. Мы приобретали универсальную горелку на дизтопливо, мазут и газ. Сейчас работаем на мазуте, затраты на выпуск тонны материала составляют 13 рублей. По дизтопливу – около 16. А вот с использованием газа – 8 рублей, что позволило бы при прошлогоднем объеме сэкономить примерно 480 тысяч. Поэтому в текущем году сделаем проектную документацию, а в следующем планируем подвести газ к промышленной территории. Это обойдется примерно в 300–400 тыс. рублей, которые окупятся за год.